Exclusive solutions
Discover our unique capabilities
Specialty OEM Polyurethane Foam Products
As a provider of specialty OEM products, our division offers customized foam solutions for a wide range of applications. From sound reducing parts for the automotive industry to packaging, sealing, and reduction of noise emissions, we have the right solution for you.
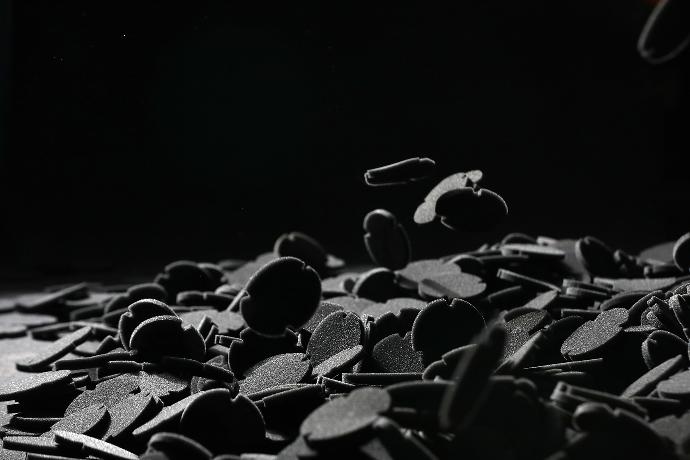
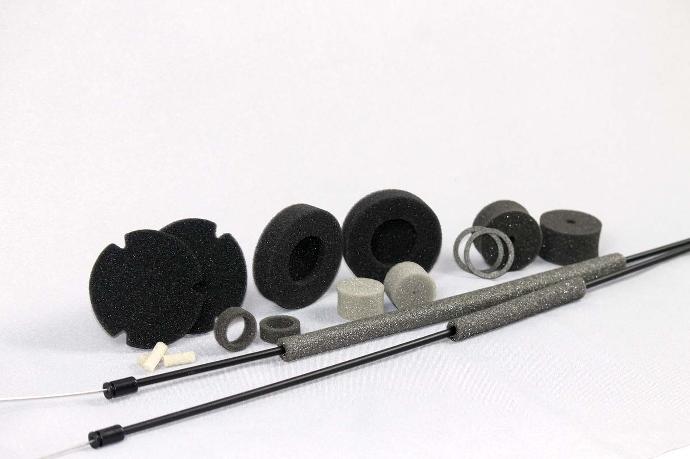
German-made, high-quality flexible polyurethane foams
Our large variety of technologies, combined with our inventory of German-made, high-quality foams, known as SchulzFoams, allows us to fulfill nearly every need. We can provide holes, 2D, 3D, and 4D shapes, cutting, machining, pressing, and stamping – you name it, we can do it.
Furthermore, our three printing technologies give you a unique range of options to further enhance your product with logos, codes, or other information.
Foam technology for automotive industry
For the automotive industry, we produce tubes made of polyurethane foam with an outside diameter of 15 and 17 mm in large batches. These are commonly used for bowden cables in seat units. Additionally, we also manufacture individual pre-cut parts for product packaging and stamping parts made from reticulated foam in various shapes and sizes.
At our company, customer satisfaction is our top priority. That's why we offer a wide range of foam solutions to meet your specific needs and requirements. Our team of experts is always available to help you find the right solution for your application.
We understand the importance of high-quality materials and precise manufacturing processes in the automotive industry. That's why we use only the best German-made foams, known for their durability and reliability. Our foams are tested to ensure they meet the highest standards of quality and safety.
Whether you require tubes, pre-cut parts, or custom shapes and sizes, our team is ready to help you find the perfect solution. We are confident that our wide range of technologies and high-quality materials will meet your needs and exceed your expectations.
If you have any questions or would like to learn more about our foam solutions, please don't hesitate to contact us. We look forward to working with you and helping you find the right solution for your application.
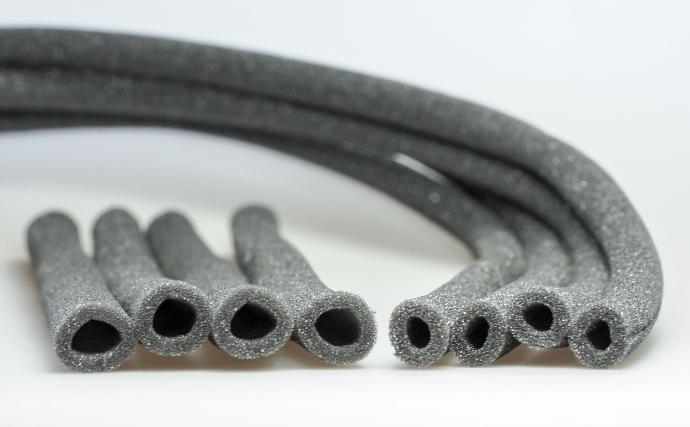
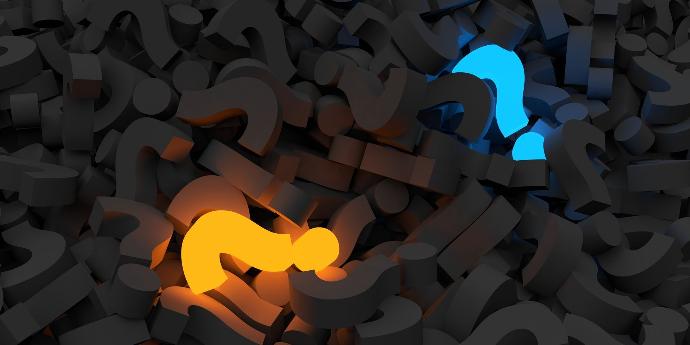
What are Polyurethane foams?
Polyurethane foam is a type of foam that is synthesized using polyol and diisocyanate. This type of foam is commonly used in a variety of applications, including bedding, furniture, and automotive products.
One of the most well-known types of polyurethane foam is memory foam. Memory foam is a type of polyurethane foam that is known for its ability to conform to the shape of a person's body, providing support and pressure relief. Memory foam is often used in mattresses and other bedding products.
In addition to memory foam, there are other types of polyurethane foam, such as high resilience foam and high density foam. These types of foam have different properties and are used in a variety of applications.
Since polyurethane foam can contain additives, manufacturers are able to create new formulas and name the resulting foam whatever they like. This means that there are many types of polyurethane foam on the market, each with its own unique characteristics.
Many memory foam mattresses are made using a combination of polyurethane foams, layered from dense on the bottom to less dense on the surface layers. This allows the mattress to provide support and pressure relief while also being comfortable to sleep on.
One potential downside of polyurethane foam is that it has a tendency to off-gas. This means that it can release volatile organic compounds (VOC) into the air, which can be harmful to people with lung conditions. If you are sensitive to VOC, it is important to do your research before purchasing a polyurethane foam or polyurethane spray foam insulation product to ensure that it is of high quality and will not off-gas.
In conclusion, polyurethane foam is a versatile and widely used type of foam that has many applications. It is known for its ability to conform to the shape of a person's body, providing support and pressure relief. However, it is significant to be aware of its potential to off-gas and to choose high-quality products to avoid any potential health risks.
The history of Polyurethane foam
PU foam is a type of foam that is synthesized using polyol and diisocyanate. This type of foam has a wide range of applications, including bedding, furniture, and automotive products.
The history of polyurethane foam dates back to 1937, when Otto Bayer and his coworkers at IG Farben in Leverkusen, Germany, first made polyurethanes. This was a significant development, as it allowed for the production of flexible foams that were not covered by patents on existing plastics.
During World War II, polyurethanes were used on a limited scale as aircraft coatings. In the 1950s, the availability of polyisocyanates allowed for the mass production of flexible polyurethane foam. This marked the beginning of the widespread use of polyurethane foam in a variety of applications.
In the 1960s, polyurethane rigid foams were used as high-performance insulation materials, thanks to the availability of chlorofluoroalkane blowing agent, inexpensive polyether polyols, and methylene diphenyl diisocyanate (MDI).
This period also saw the introduction of urethane-modified polyisocyanurate rigid foams, which offered even better thermal stability and flammability resistance.
In the 1980s, the development of water-blown microcellular flexible foams allowed for the use of polyurethane foams in automotive applications, such as seating, head and arm rests, and headliners.
The use of polyurethane foams has continued to evolve, with the introduction of new blowing agents like carbon dioxide and the development of reinforced RIM (RRIM) technology. Today, polyurethane foam is a widely used material in many industries.
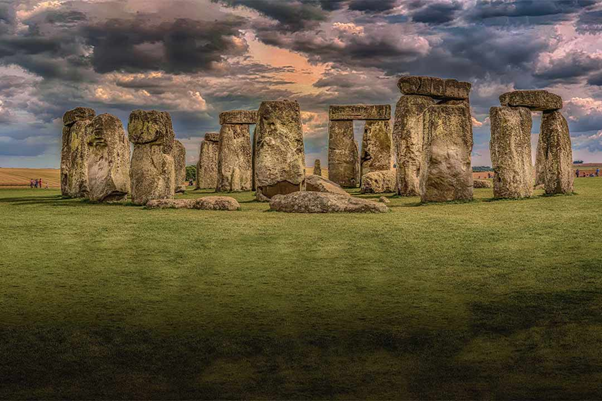
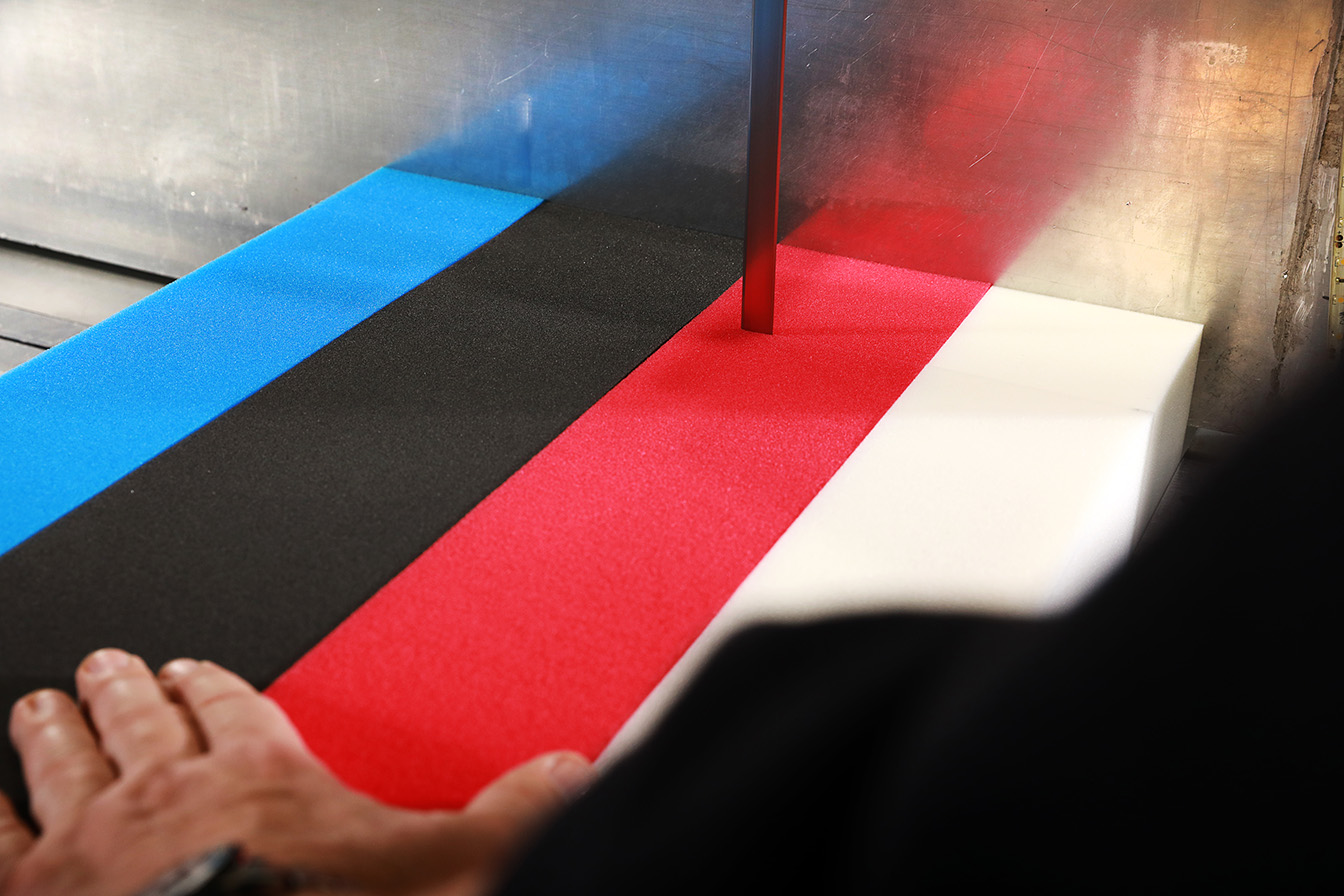
Raw materials
The main ingredients used to make polyurethane foam are di- and tri-isocyanates and polyols. These materials are mixed together in a specific ratio to create the desired properties of the foam.
Additional materials can be added to the mixture to aid in the processing of the polymer or to modify the foam properties. For example, flame retardants can be added to make the foam more resistant to fire. Other materials, such as fillers or blowing agents, can be added to change the density or thermal insulation properties of the foam.
The process of making polyurethane foam begins with the mixing of the polyol and isocyanate components. This mixture is then poured into a mold and allowed to expand, creating the foam. The resulting foam can be either open cell or closed cell, depending on the specific formulation of the mixture.
Open cell foams have a more porous structure, which allows air to flow through the foam. This makes them softer and more flexible than closed cell foams, which are denser and have a more solid structure.
Once the foam has been formed, it can be cut into the desired shape and size. This allows for the production of a wide range of products, from foam cushions and mattresses to automotive parts and packaging materials.
Overall, the process of making polyurethane foam involves the careful mixing of specific ingredients to create a polymer with the desired properties. This versatile material has a wide range of applications and continues to be an important material in many industries.
Conclusion
We are able to produce
OEM products for a wide range of applications with the help of our large
variety of technologies. If you have any needs for customized foam
solutions, we will likely be able to fulfill your wishes.
We specialize in
automotive industry sound reduction parts, but we also produce other
types of packaging and sealing solutions. In addition, we can machine,
press, stamp, and cut shapes into 2D, 3D, and 4D forms. Our three
printing technologies give you extra options to increase the value of
your product by adding logos, codes, or information.
Automotive industry tubes
are one example of what we can mass produce – 15 mm and 17 mm outside
diameters made from polyurethane foam. Contact us today if you require
an OEM product fulfilled!